With Mühlberger Engineering's warehouse management system, you have all salt and brine storage facilities effortlessly under control.
From manually integrated salt silos to our convenient Topautomatik system, whether it's a simple brine tank or a fully automated Turbosol for brine storage - our hardware and software ensure that you always have an overview of your stock, from your desktop in the office or from your smartphone with Salzmanager Dashboard.
All processes, such as salt and brine refills and withdrawals, are recorded and are visible in real time in the Salzmanager.
Each user is identified by an active transponder or RFID chip or smartphone, and their actions are recorded.
Suppliers can confirm their delivery via a QR code on the silo.
Silo weighing - systems
Strain gauges have proven particularly useful for silo weighing. Alternatively, load cells can also be used.

STRAIN GAUGES (SYSTEM MÜHLBERGER)
Weighing using strain gauges is reliable, accurate and economical. Gauges can also be installed on existing silos at a later stage, often even without emptying the silo. [Accuracy: +/- 2%]

LOAD CELLS
Load cells can also be installed later, but the silo must be emptied. [Accuracy: +/- 2%]
Stages of silo automation expansion
Automation can be integrated into new silos and brine tanks as early as the planning phase. Existing systems can be easily upgraded - depending on the structure, minor conversion work may be required.
Below we present the various expansion stages of silos and brine tanks as well as the respective processes:
Expansion stages silo
Weighing with Weight Display
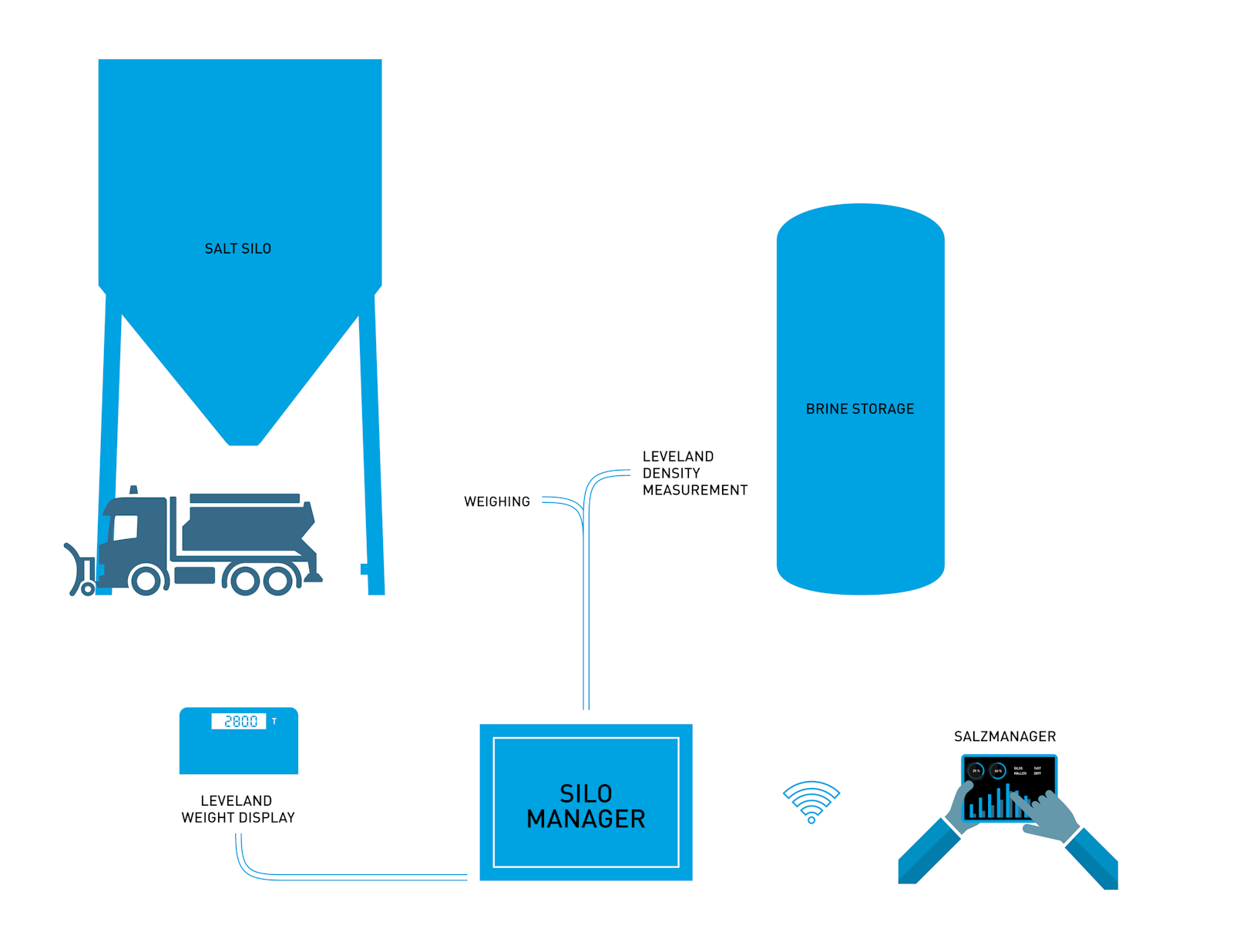
Process
The silo level is recorded using strain gauges or load cells and displayed on a screen
The silo level is transmitted to the SalzManager and further processed
Semi Automation
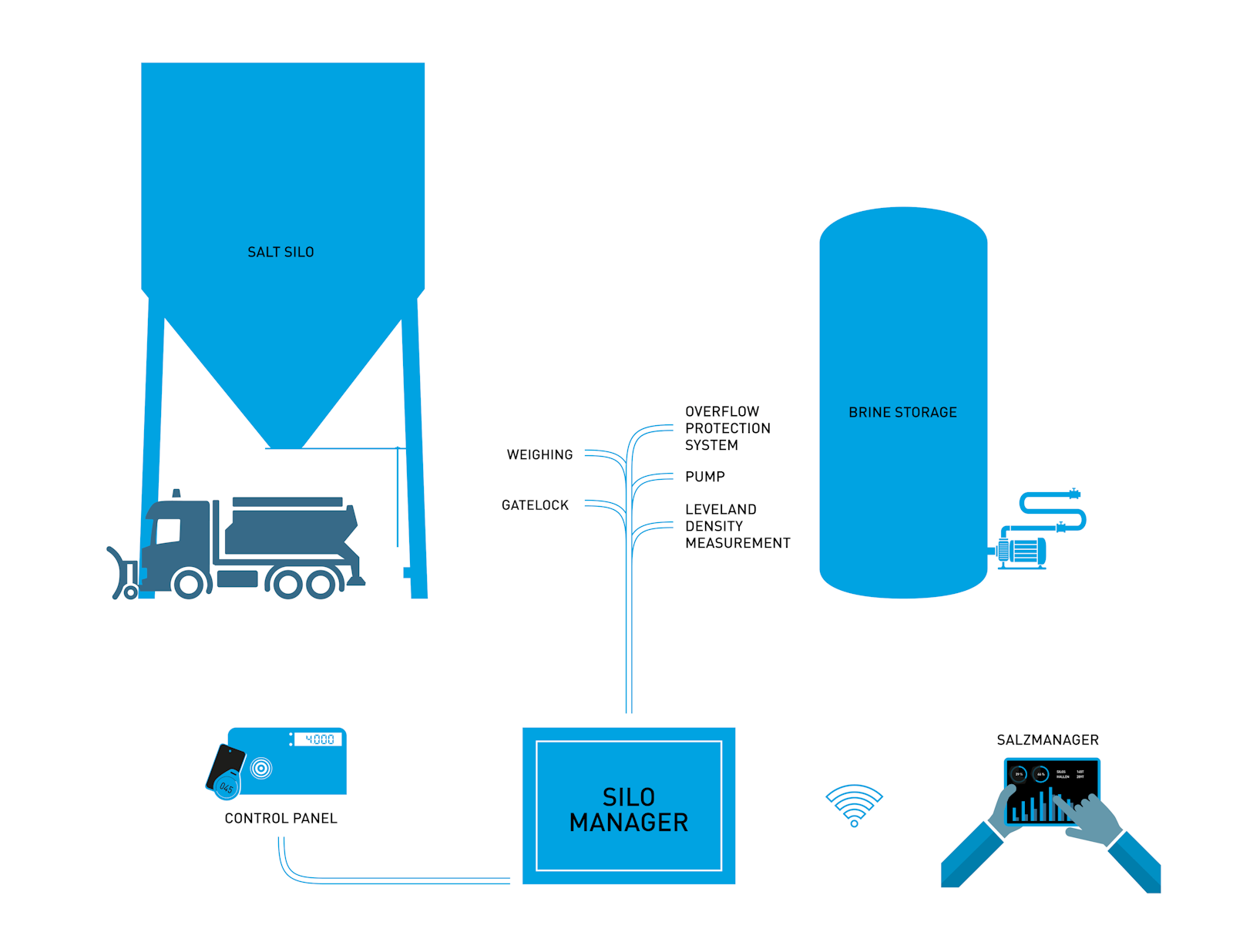
In addition to basic visualization, the semi-automatic system provides a controlled release of silo discharge
Process
The operator authenticates at the silo using a transponder or smartphone
The silo slide gate is released via a magnetic lock
The slide gate can be manually opened using the control rod to fill the vehicle
After the filling process is completed, the control rod locks into place, the process is concluded, and the data is recorded and processed further in the SalzManager for additional evaluations
Full Automation
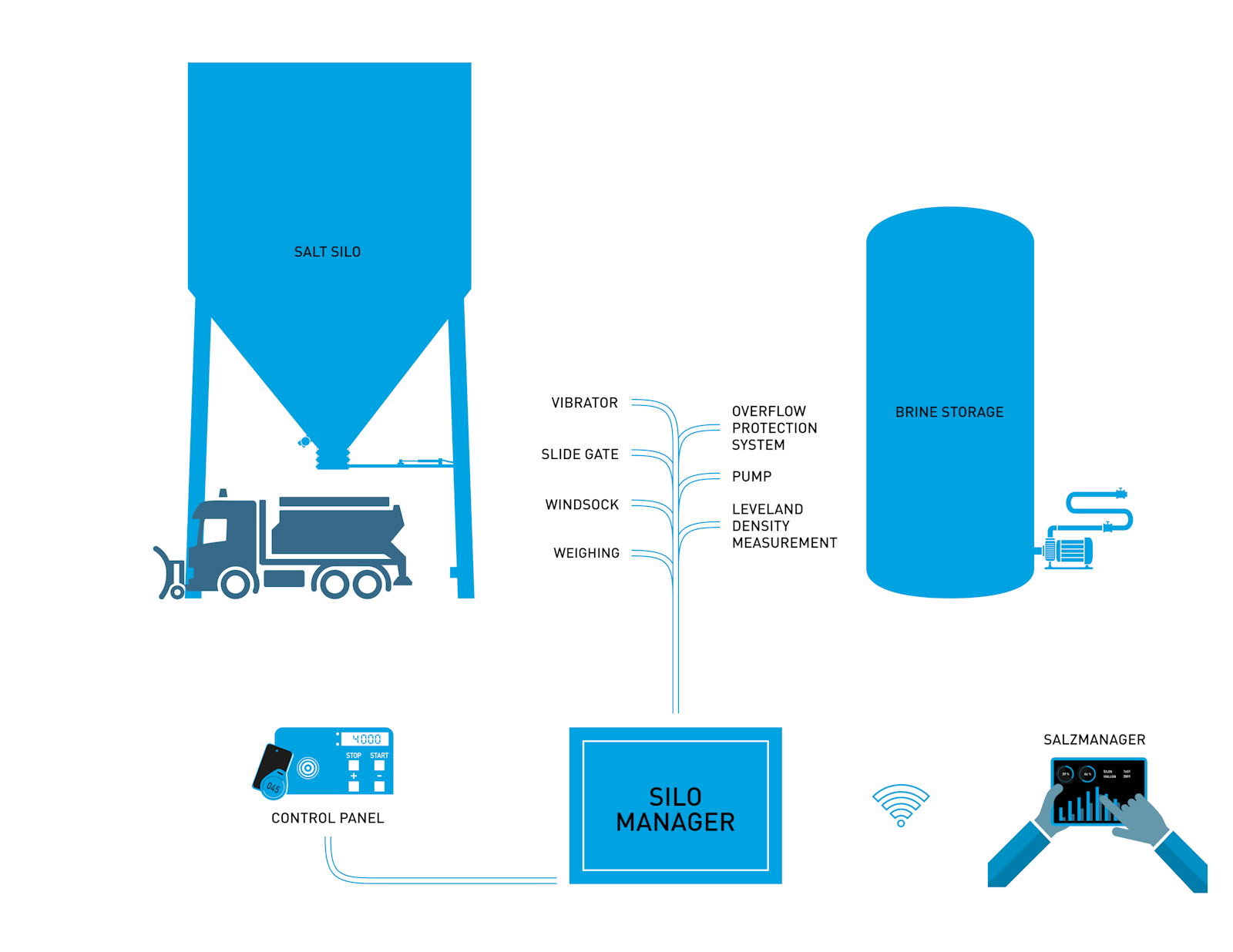
In addition to the weighing and semi-automatic functions, the fully automatic system provides automatic control of the silo slide gate and the flexible hose
Process
The operator authenticates at the control unit using a transponder or smartphone and can specify the withdrawal quantity
By pressing the start button, the automatic discharge process begins:
The flexible hose moves to the preset vehicle height (optional)
The slide gate opens and closes automatically after the selected quantity has been discharged (the discharge process can be interrupted at any time by pressing the stop button)
The vibrator at the silo outlet starts automatically at the beginning of the discharge to break up any salt clumps
3. After the selected quantity has been dispensed, the silo slide gate closes, the flexible hose returns to its starting position, and the process is recorded and further processed in the SalzManager for additional evaluations
Topautomatik - Discharging without leaving the vehicle cabin
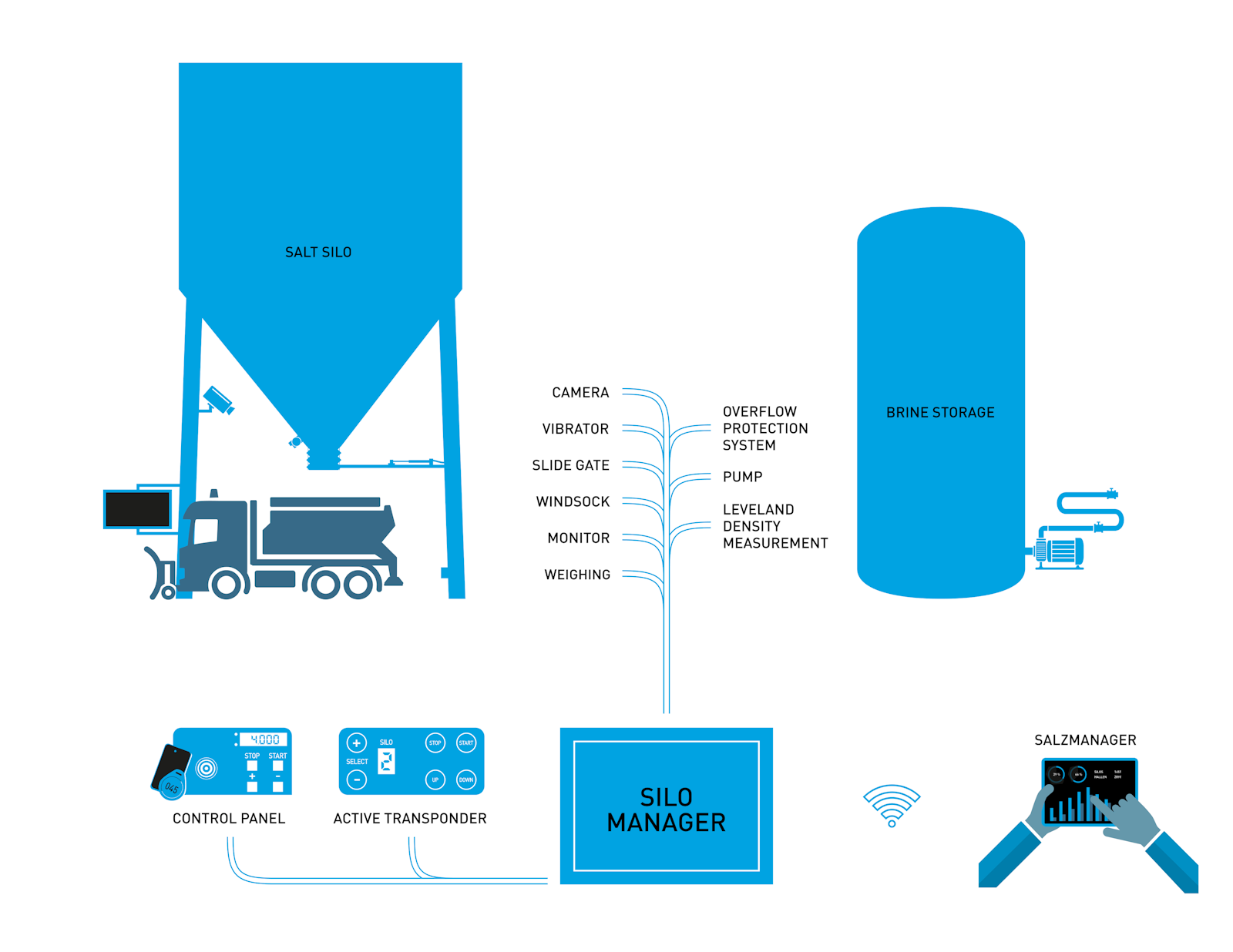
In addition to full automation, it enables discharging without leaving the vehicle cabin, ensuring maximum efficiency and safety. Developed in collaboration with Blumer-Lehmann.
Process
The vehicle drives under the silo, and the operator is authenticated via the control unit (active transponder) installed in the vehicle and can select the preferred withdrawal quantity
For precise vehicle positioning, the camera and monitor are activated
The monitor displays the camera image of the loading area with a positioning cross as well as the current silo fill level
The driver does not need to leave the cabin: starting and stopping the discharge process is done via the control unit in the vehicle (active transponder) or automatically after the selected quantity has been discharged
Additional safety is provided by the hydraulic silo slide gate, which automatically closes in the event of malfunctions or power failures
Expansion stages salt brine dispensing point
Brine discharge with level indicator
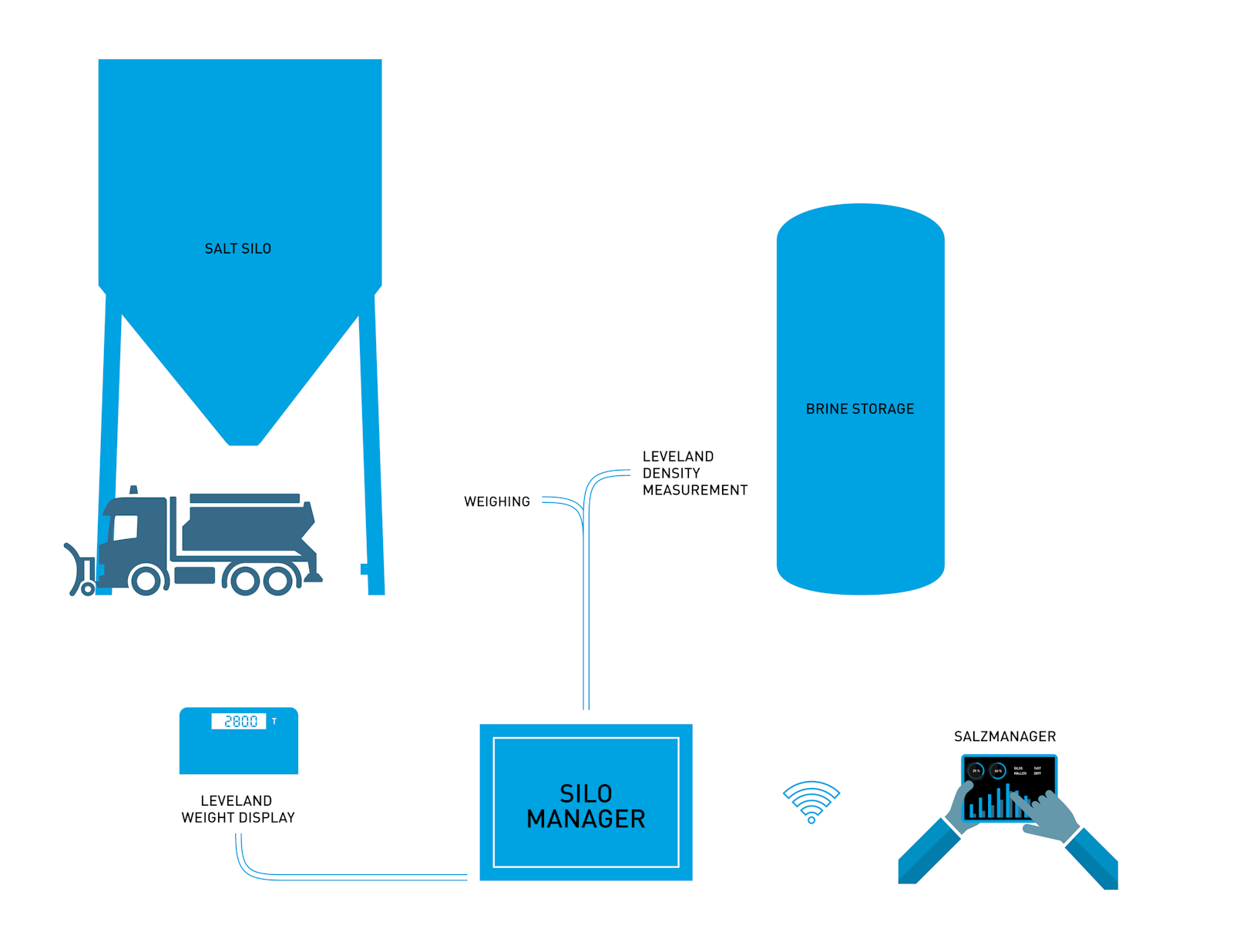
Process
The fill level and concentration of the preparation and storage tanks are recorded and displayed on a screen
The recorded values are transmitted to the SalzManager and further processed
Brine discharge with semi-automatic system
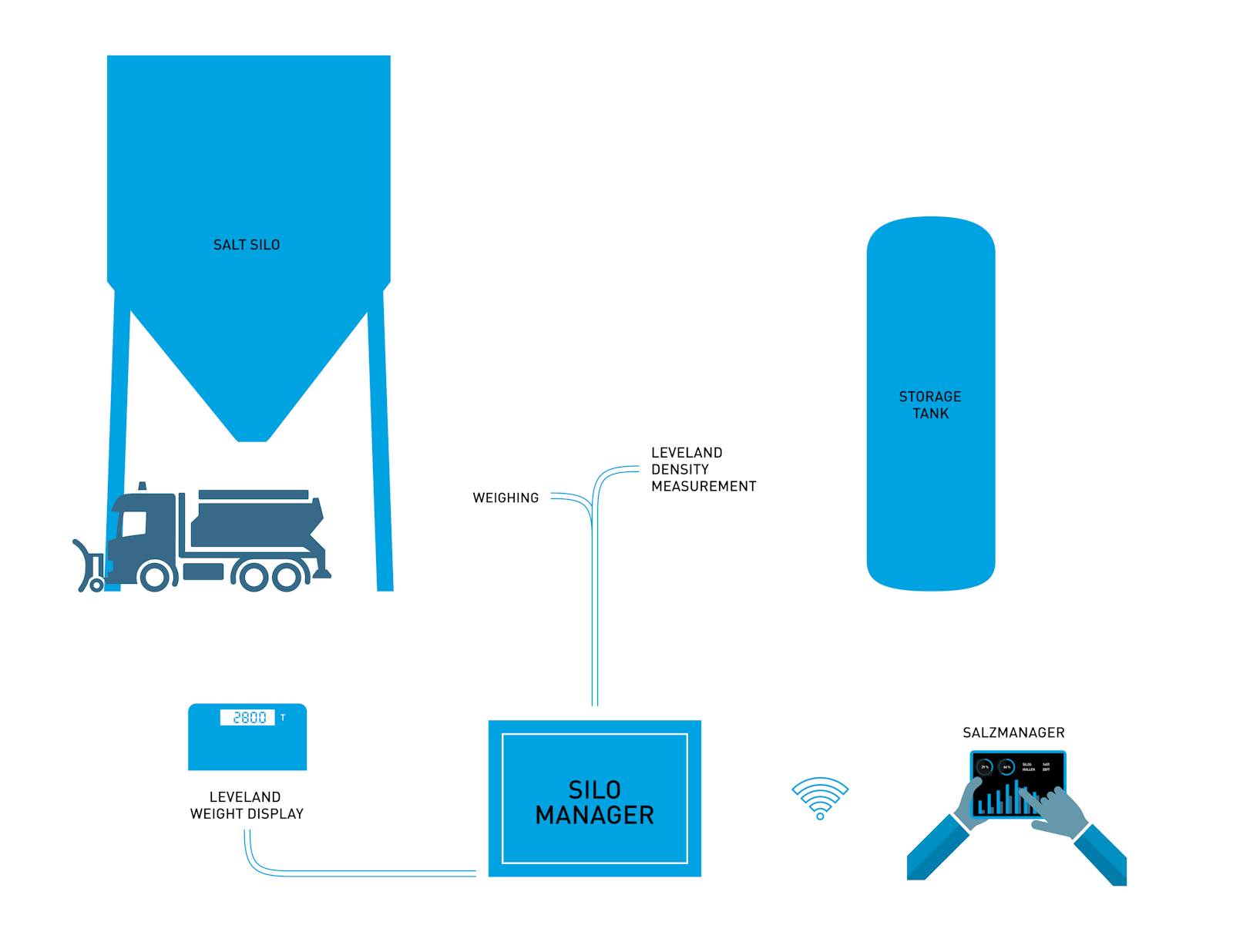
In addition to the functions of discharge with level display, the semi-automatic system offers controlled release of the discharge:
Process
The operator authenticates at the brine system using a transponder or smartphone
The pump is released and can be manually switched on or off
After completion, the process is recorded and further processed in the SalzManager for additional evaluations
Brine discharge with fully automatic system
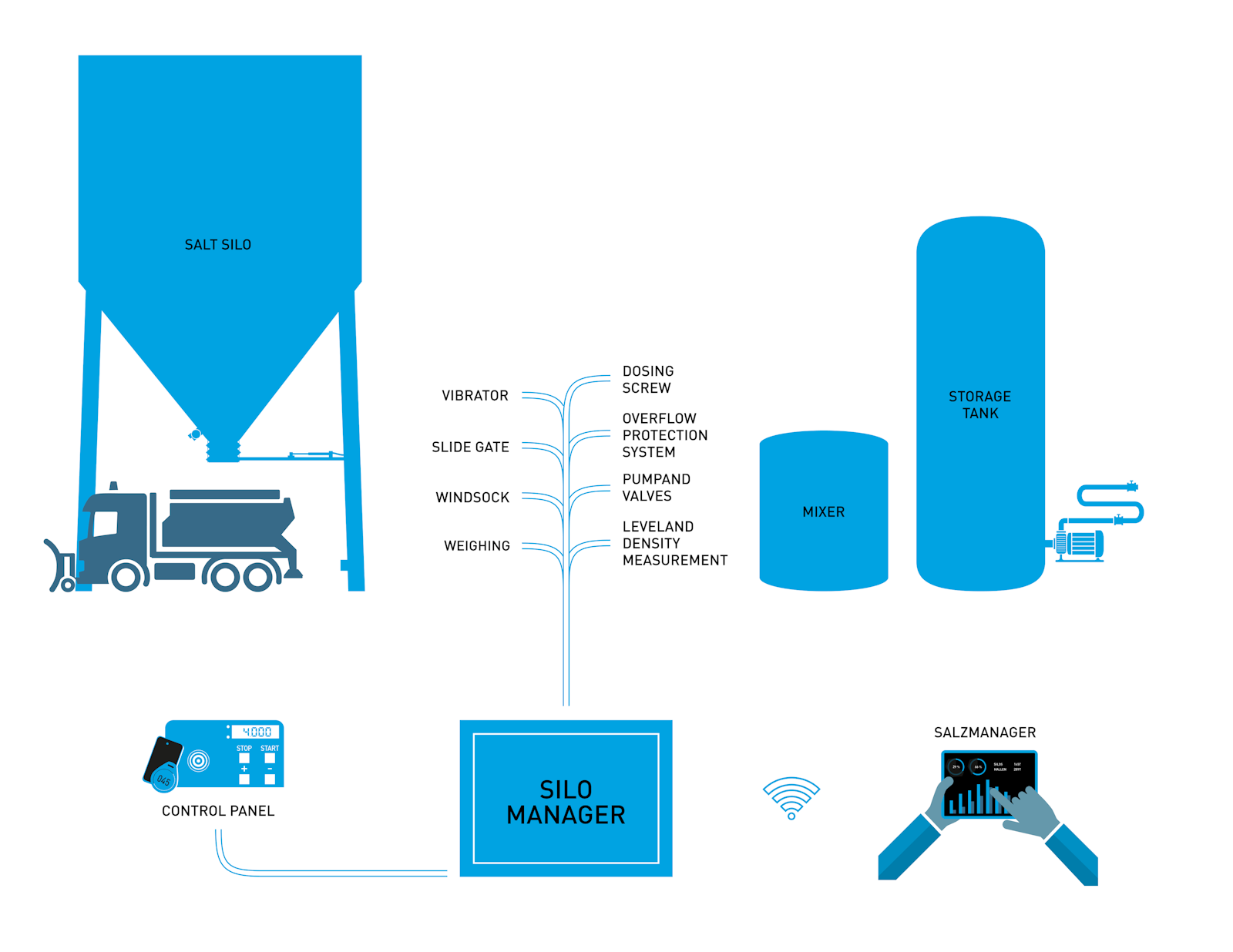
In addition to the semi-automatic discharge, it offers the option to select the desired discharge quantity with automatic pump activation and deactivation
Process
The operator authenticates at the brine system control unit using a transponder or smartphone and can specify the desired discharge quantity
By pressing the start button, the pump is automatically turned on; the process can be interrupted or ended at any time by pressing the stop button
After the selected quantity has been dispensed, the pump automatically turns off, and the process is recorded and further processed in the SalzManager for additional evaluations
Product images

At the Silomat operating unit, the user can unlock the silo via an RFID chip and control product withdrawal and windsock.

RFID chips are used for user identification and as silo keys. They can be assigned to people, vehicles or even specific sections of roads through key management in the Salzmanager.

With the Active Transponder (only availble with the Topautomatic system), the silo can be conveniently controlled from the vehicle cab.